Production and Technology
Pioneering sustainability
We began implementing recycling technology into our production decades ago. By the 1980s, we had decommissioned our last blast furnace, completing the transition to using recycled steel scrap as our primary raw material and eliminating the need for iron ore.
100 % of our steel is made from recycled steel scrap. Scrap is meticulously sorted with the magnetic separator to ensure it closely matches the desired chemical composition.
The scrap is melted in an Electric Arc Furnace. Depending on the desired steel grade, the material is processed in either an Argon Oxygen Decarburization or Vacuum Oxygen Decarburization converter. After refining, the steel is cast into ingots or on a continuous casting machine, preparing it for forging or rolling. The steel then undergoes heat treatment and finishing processes to achieve the necessary mechanical and physical properties.
Throughout the production process, our in-house laboratories conduct thorough analyses to guarantee that all quality standards are met. This ensures that every piece of steel we produce meets the highest benchmarks for performance and reliability.
Green Evolution
Adoption of EAFs and the use of recycled steel scrap as primary raw material allowed us to achieve CO₂ emissions levels nearly four decades ago that are now considered a benchmark for our industry.
And now, we’re doing it even better!
Our three dedicated in-house R&D departments, equipped with cutting-edge technology and staffed by over 90 experts, ensure that we continually push the boundaries of quality and performance in our products. This relentless pursuit of innovation, combined with our dedication to sustainability and investment in Best Available Technologies, guarantees that our products are of the highest quality and have a smaller impact on the environment.
To meet the goal of carbon neutrality by 2050, we are investing in Best Available Technologies and continuously optimizing our production processes to enhance efficiency. We are enhancing our furnaces with better insulation and advanced burning systems and upgrading to recuperative, regenerative, and oxy-fuel burners. Transitioning from gas to electricity and hydrogen, we are significantly cutting energy consumption and CO₂ emissions. Additionally, we are partnering with local municipalities to reuse waste heat, creating advanced energy communities.
*Scope 1
*Scope 1
SIJ Acroni
SIJ Acroni produces steel by recycling scrap in an electric arc furnace, casting it on a continuous caster, and rolling it into high-quality flat-rolled steel products up to 2500 mm in width. The company consists of five plants: the raw materials department, steel mill, hot rolling mill, cold rolling mill, and quarto plate processing. Core production programs include stainless steel quarto plates, special steels (high-strength and wear-resistant steels), non-oriented electrical plates, alloyed tool steels, and more.
SIJ Metal Ravne
SIJ Metal Ravne produces steel by recycling scrap in an electric arc furnace, casting it into ingots, and rolling or forging it into high-quality long steel products. Their own forging shop, rolling mill, ESR remelting furnaces, and a wide range of heat treatment and machining options allow them to produce a diverse array of more than 200 steel grades in different dimensions and forms.
Got a question?
We've got the answers! Our team is here to help you with anything you need.
Executive Director of Production, Technology and Investment
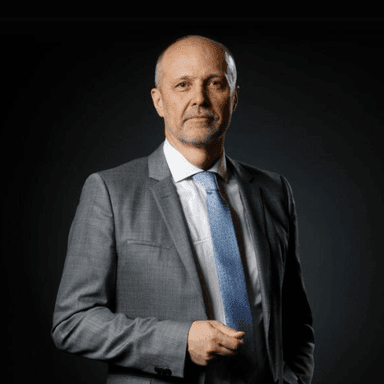